Elevator exterior lock sector key triangle lock accessories
Description
Product Type | customized product | |||||||||||
One-Stop Service | Mold development and design-submit samples-batch production-inspection-surface treatment-packaging-delivery. | |||||||||||
Process | stamping,bending,deep drawing,sheet metal fabrication,welding,laser cutting etc. | |||||||||||
Materials | carbon steel,stainless steel,aluminum,copper,galvanized steel etc. | |||||||||||
Dimensions | according to customer's drawings or samples. | |||||||||||
Finish | Spray painting, electroplating, hot-dip galvanizing, powder coating, electrophoresis, anodizing, blackening, etc. | |||||||||||
Application Area | Auto parts, agricultural machinery parts, engineering machinery parts, construction engineering parts, garden accessories, environmentally friendly machinery parts, ship parts, aviation parts, pipe fittings, hardware tool parts, toy parts, electronic parts, etc. |
Welding process
The hardware welding process mainly includes the following steps:
1. Select appropriate welding equipment and welding materials: Determine the welding method and parameters such as welding current, voltage, and welding speed according to the characteristics of the metal materials to be welded. When selecting welding materials, consider the requirements of the weld and select a suitable welding rod or wire.
2. Preparation before welding: This includes cleaning and derusting the welded parts to ensure that the welding surface is free of impurities and oil. At the same time, pre-treatment is carried out, such as trimming, cleaning and rust removal, mark inspection, etc., to ensure that the location of the weld meets the welding requirements.
3. Assembly and alignment: Place the pieces to be welded on the work support and align them. Excessive displacement should be avoided during the alignment process to avoid directional stress after welding.
4. Clamping: Generally, machine clamps or manual clamps are used for clamping to ensure that the welding parts will not be deformed or miss welded.
5. Welding: According to different materials, select appropriate welding electrodes and process parameters, and perform welding according to the welding process requirements. During the welding process, the appropriate welding speed and angle must be maintained so that the welding material can fully melt and flow into the weld.
6. Post-welding treatment: This includes trimming the welds, which can be done using a grinder or hand tools. To clean welding slag, you can use a scraper or weld cleaner to remove the welding slag generated during the welding process. Cool the weld and adjacent areas to prevent thermal stresses.
7. Inspection and evaluation: After welding is completed, the welded joints must be inspected to ensure that the welding quality meets the requirements.
In addition, we also need to pay attention to the quality control of welding materials, including the selection, storage, delivery, and receipt of welding materials. At the same time, the protective gas and welding solidification speed must be controlled during the welding process, and welding defects such as surface defects, internal defects, dimensional deviations, etc. must be detected and evaluated.
The above are the basic steps and precautions for the hardware welding process. The specific operations may be adjusted due to different equipment and processes. During the entire welding process, various parameters and operating steps need to be strictly controlled to ensure product quality and stability.
Quality management
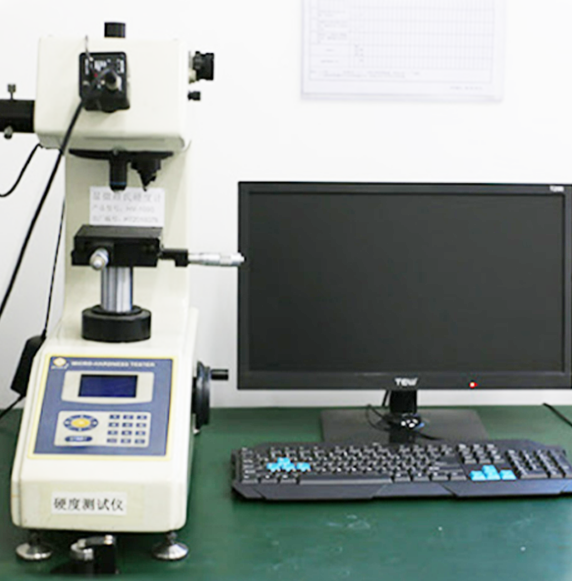
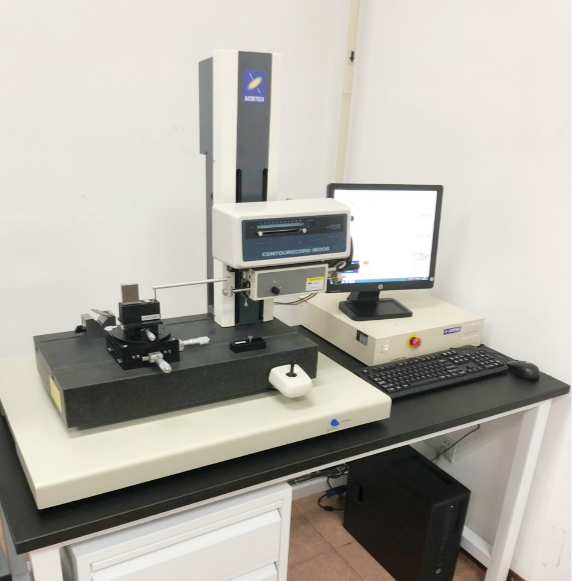
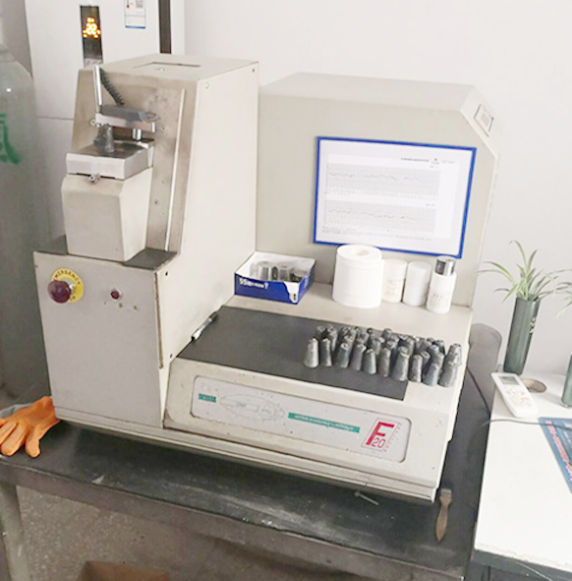
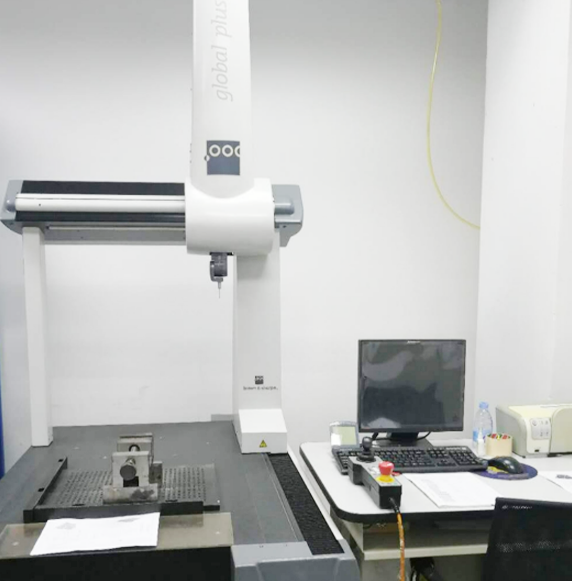
Vickers hardness instrument.
Profile measuring instrument.
Spectrograph instrument.
Three coordinate instrument.
Shipment Picture
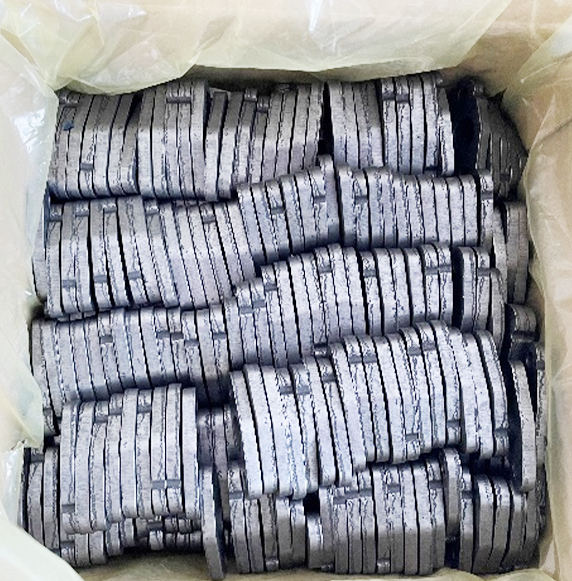
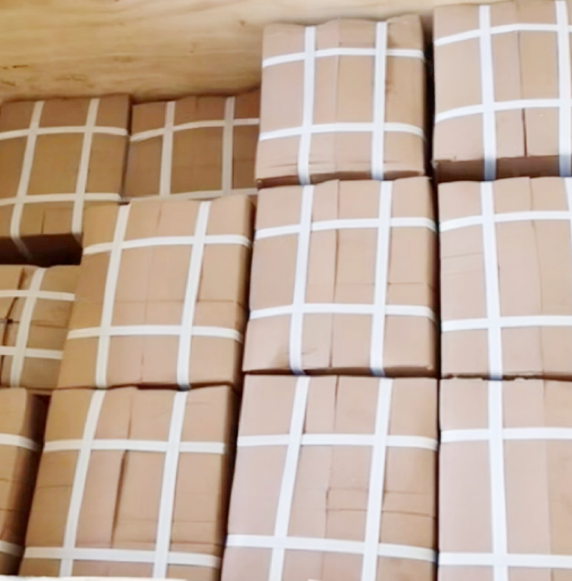
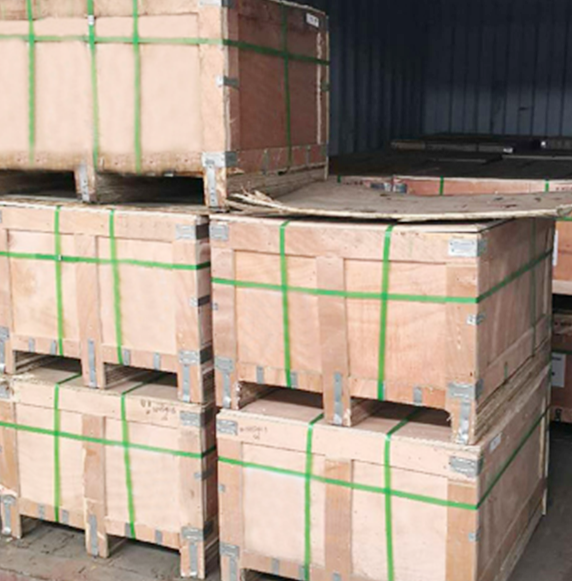
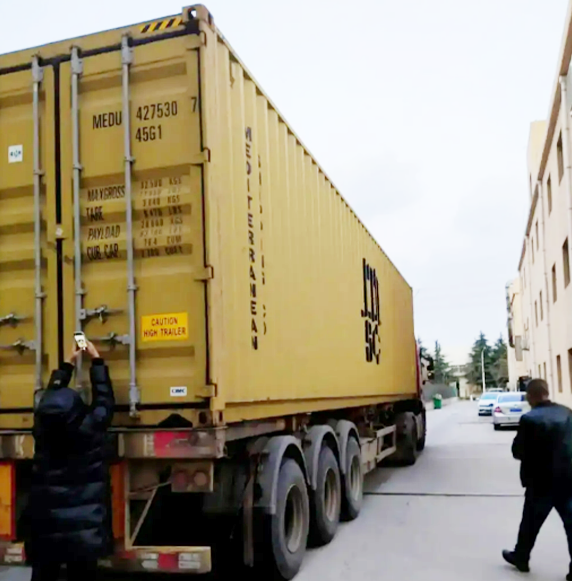
Production Process
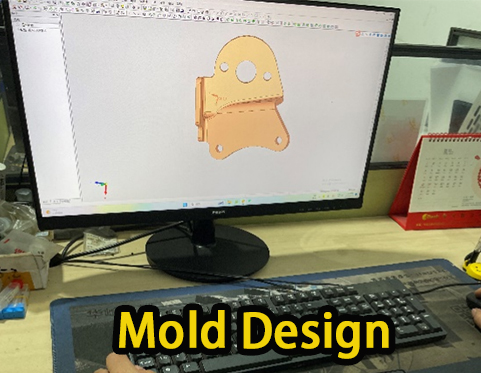
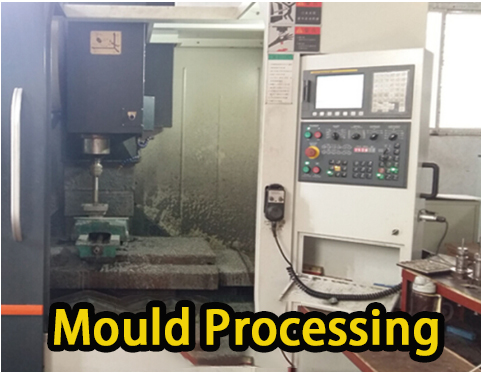
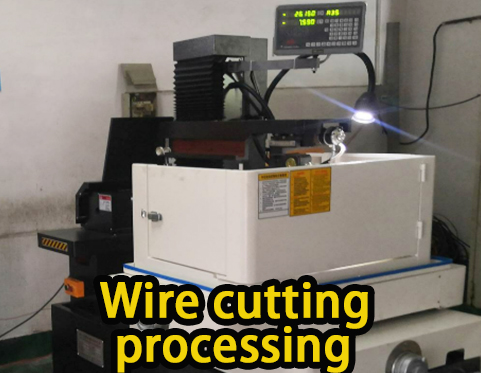
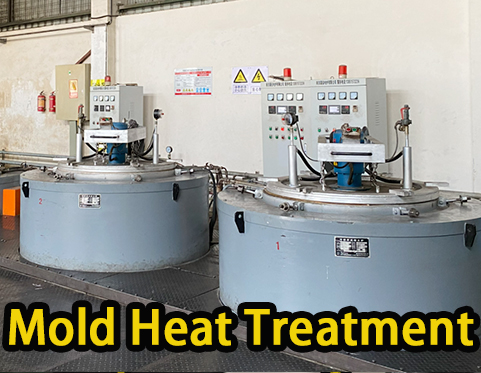
01. Mold design
02. Mould Processing
03. Wire cutting processing
04. Mold heat treatment
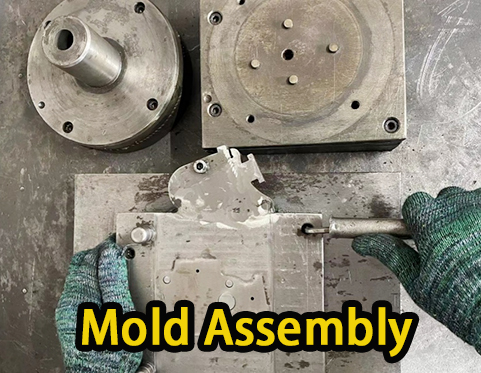
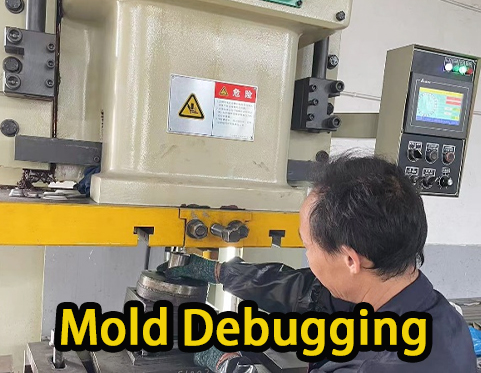
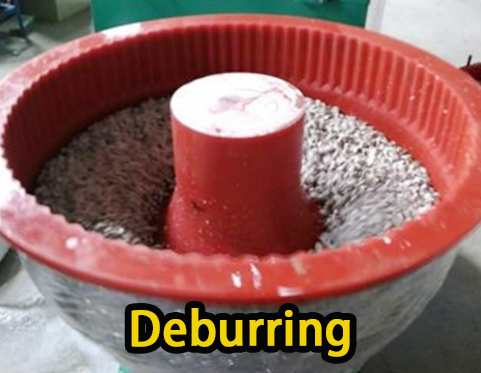

05. Mold assembly
06. Mold debugging
07. Deburring
08. electroplating
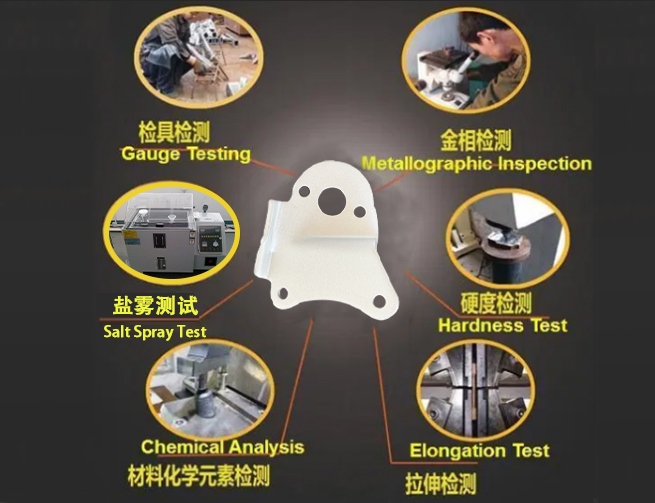
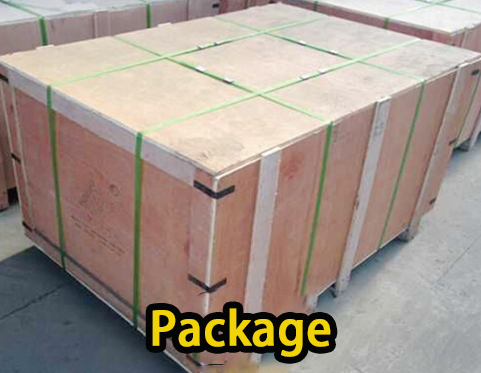
09. Product Testing
10. Package
Our service
1. Skilled research and development team – Our engineers create original designs for your products to help your business.
2. Quality Supervision Team: To guarantee that every product functions properly, it is rigorously checked before shipping.
3. Effective logistics team: until the goods is delivered to you, safety is ensured by timely tracking and tailored packaging.
4. An independent after-sales team that offers clients prompt, expert assistance around-the-clock.
5. Skilled sales team: You will receive the most professional expertise to enable you to conduct business with clients more effectively.
FAQ
Q: Are you a trading company or manufacturer?
A: We are manufacturer.
Q: How to get the quote?
A: Please send your drawings (PDF, stp, igs, step...) to us by email , and tell us the material, surface treatment and quantities, then we will make a quotation to you.
Q: Can I order just 1 or 2 pcs for testing?
A: Yes, of course.
Q. Can you produce according to the samples?
A: Yes, we can produce by your samples.
Q: How long is your delivery time?
A: 7~ 15 days, depends on the order quantities and product process.
Q. Do you test all your goods before delivery?
A: Yes, we have 100% test before delivery.
Q: How do you make our business long-term and good relationship?
A:1. We keep good quality and competitive price to ensure our customers benefit ;
2. We respect every customer as our friend and we sincerely do business and make friends with them, no matter where they come from.