Custom Anodized Aluminum Parts Stamped Parts
Description
Product Type | customized product | |||||||||||
One-Stop Service | Mold development and design-submit samples-batch production-inspection-surface treatment-packaging-delivery. | |||||||||||
Process | stamping,bending,deep drawing,sheet metal fabrication,welding,laser cutting etc. | |||||||||||
Materials | carbon steel,stainless steel,aluminum,copper,galvanized steel etc. | |||||||||||
Dimensions | according to customer's drawings or samples. | |||||||||||
Finish | Spray painting, electroplating, hot-dip galvanizing, powder coating, electrophoresis, anodizing, blackening, etc. | |||||||||||
Application Area | Auto parts, agricultural machinery parts, engineering machinery parts, construction engineering parts, garden accessories, environmentally friendly machinery parts, ship parts, aviation parts, pipe fittings, hardware tool parts, toy parts, electronic parts, etc. |
Types of stamping
We offer single and multistage, progressive die, deep draw, fourslide, and other stamping methods to ensure the most effective method for manufacturing your products. Xinzhe’s experts can match your project with the appropriate stamping by reviewing your uploaded 3D model and technical drawings.
- Progressive Die Stamping uses multiple dies and steps to create deeper parts than would typically be achievable through single dies. It also enables multiple geometries per part as they go through various dies. This technique is best suited to high volume and large parts such as those in the automotive industry. Transfer die stamping is a similar process, except progressive die stamping involves a workpiece attached to a metal strip pulled through the entire process. Transfer die stamping removes the workpiece and moves it along a conveyor.
- Deep Draw Stamping creates stampings with deep cavities, like enclosed rectangles. This process creates rigid pieces since the extreme deformation of the metal compresses its structure into a more crystalline form. Standard draw stamping, which involves shallower dies used to shape the metal, is also commonly utilized.
- Fourslide Stamping shapes parts from four axes instead of from one direction. This method is used to manufacture small intricate parts including electronics components such as phone battery connectors. Offering more design flexibility, lower production costs, and faster manufacturing times, fourslide stamping is popular in aerospace, medical, automotive, and electronics industries.
- Hydroforming is an evolution of stamping. Sheets are placed on a die with a bottom shape, while the upper shape is a bladder of oil that fills to high pressure, pressing the metal into the shape of the lower die. Multiple parts can be hydroformed simultaneously. Hydroforming is a quick and accurate technique, though it requires a trim die to cut the parts out of the sheet afterward.
- Blanking cuts pieces out from the sheet as an initial step before forming. Fineblanking, a variation of blanking, makes precise cuts with smooth edges and a flat surface.
- Coining is another type of blanking that creates small round workpieces. Since it involves significant force to form a small piece, it hardens the metal and removes burrs and rough edges.
- Punching is the opposite of blanking; it involves removing material from the workpiece instead of removing material to create a workpiece.
- Embossing creates a three-dimensional design in the metal, either raised above the surface or through a series of depressions.
- Bending happens on a single axis and is often used to create profiles in U, V, or L shapes. This technique is accomplished by clamping one side and bending the other over a die or pressing the metal into or against a die. Flanging is bending for tabs or parts of a workpiece instead of the whole part.
Quality management
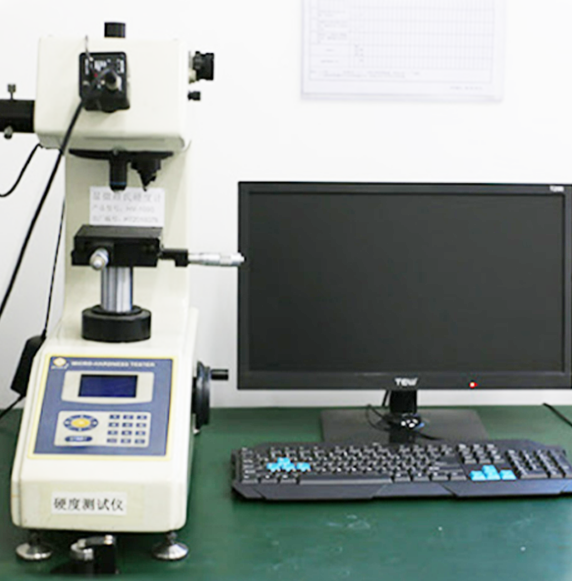
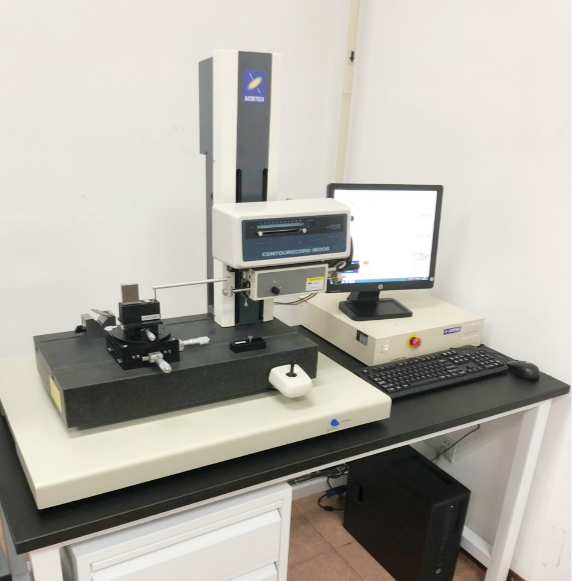
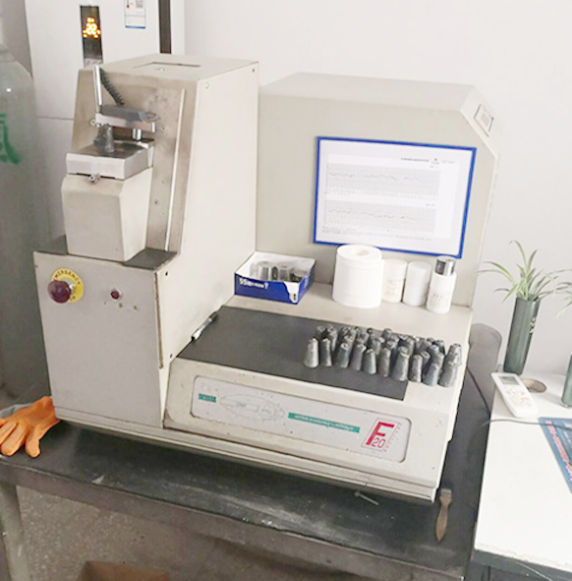
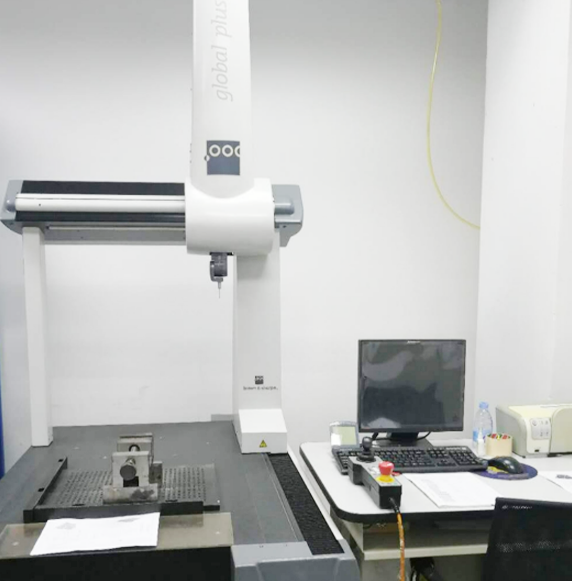
Vickers hardness instrument.
Profile measuring instrument.
Spectrograph instrument.
Three coordinate instrument.
Shipment Picture
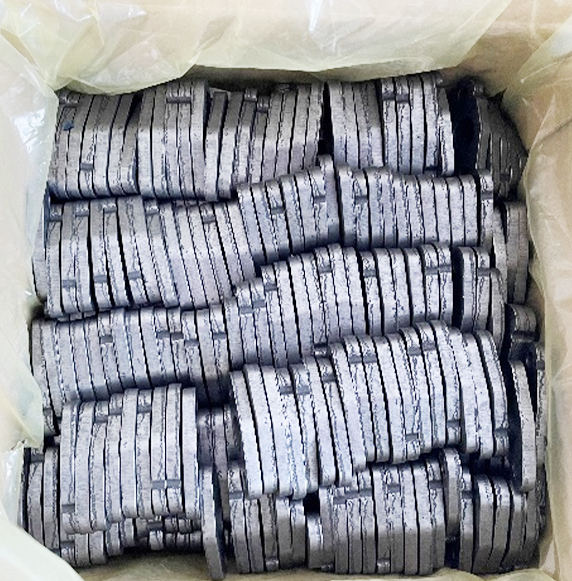
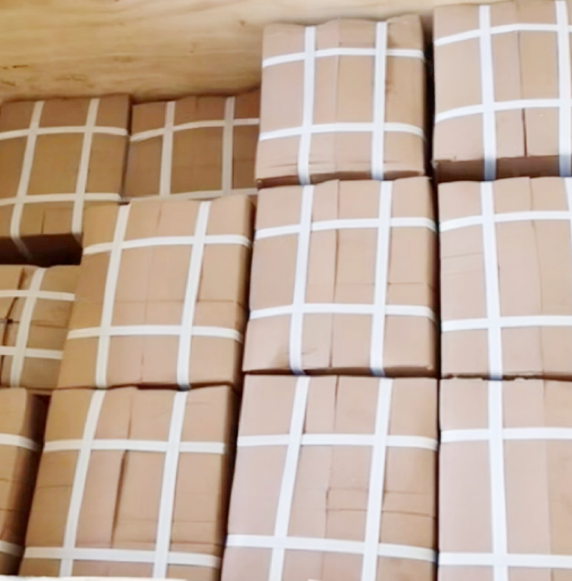
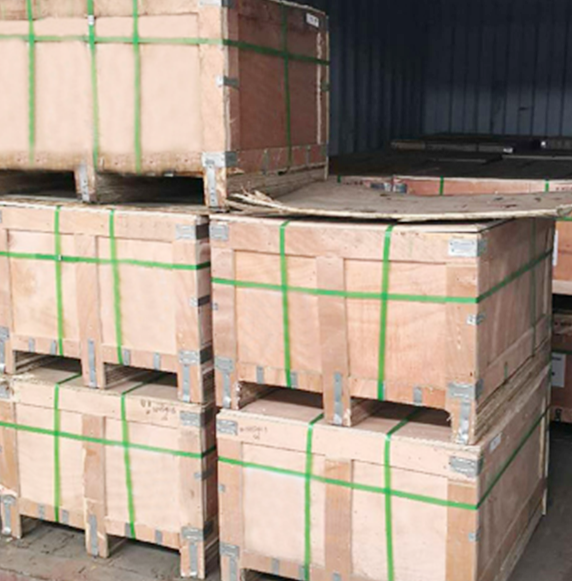
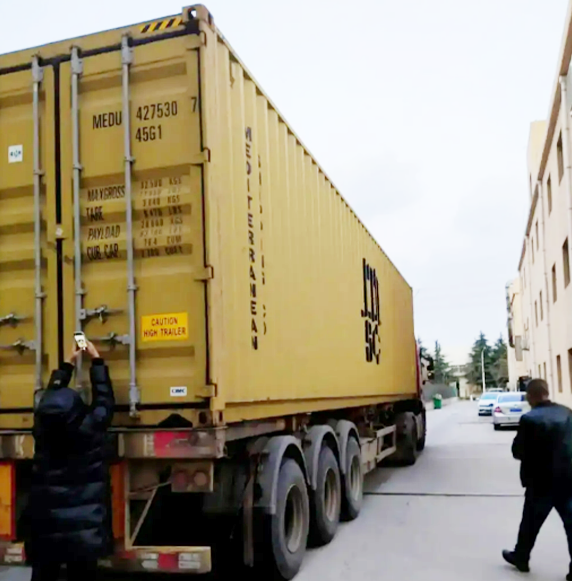
Production Process
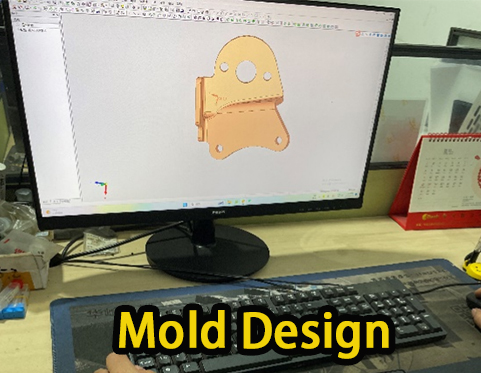
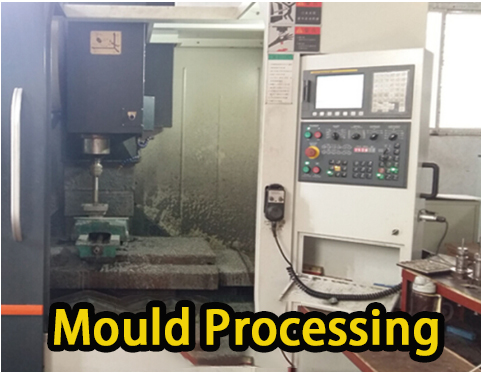
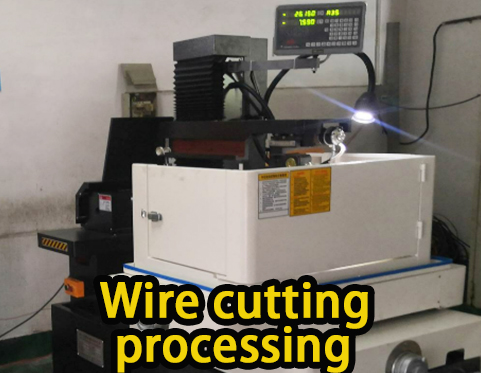
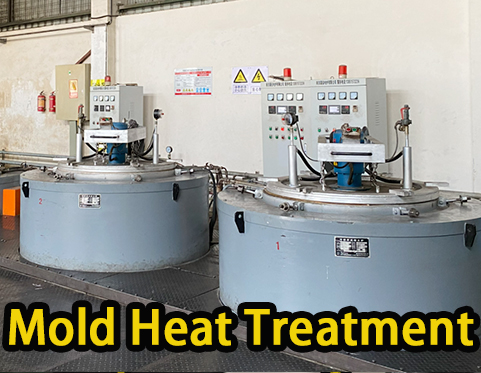
01. Mold design
02. Mould Processing
03. Wire cutting processing
04. Mold heat treatment
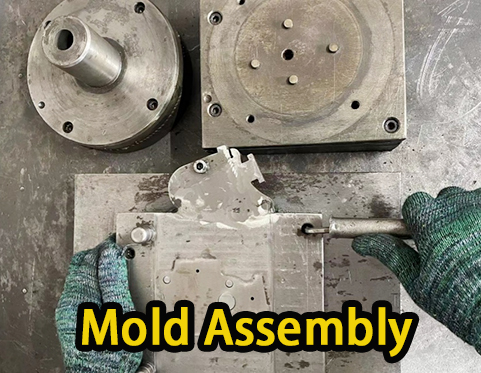
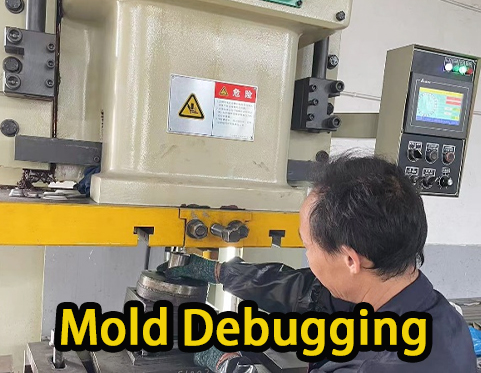
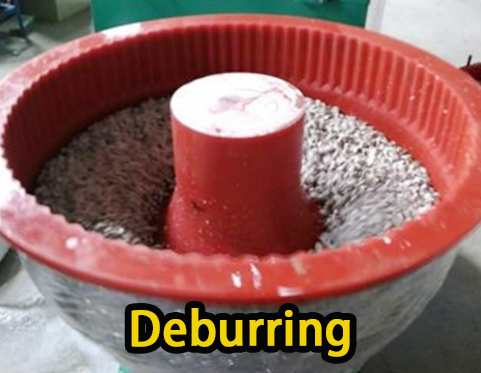

05. Mold assembly
06. Mold debugging
07. Deburring
08. electroplating
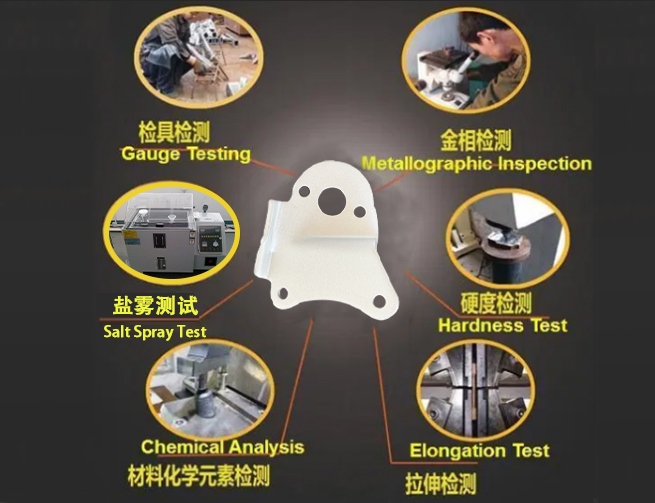
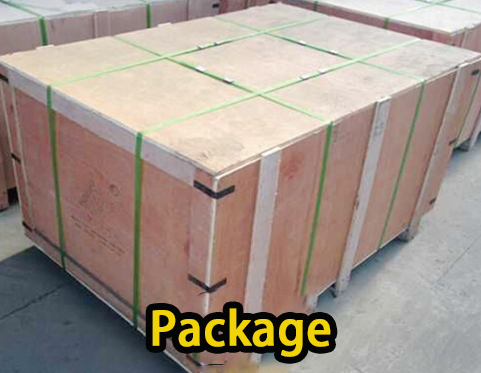
09. Product Testing
10. Package
The Stamping Process
Surface treatment process of aluminum stamping parts:
In the stamping industry, aluminum stamping parts are also a very common metal stamping part. Common surface treatment methods for aluminum stamping parts are:
1.Anodizing
Anodizing can effectively make up for the lack of surface hardness and wear resistance of aluminum stamping parts. It can also greatly increase the use time of aluminum stamping parts and make the product look more beautiful. Today, anodizing has become a commonly used surface treatment method for aluminum stamping products. Anodizing refers to the electrochemical oxidation of metals or alloys. Aluminum and its alloys form an oxide film on the aluminum product (anode) due to the effect of electric current applied in the corresponding electrolyte and specific process conditions.
2.Sandblasting
Sandblasting is generally an intermediate process for surface treatment of aluminum stamping parts. After aluminum stamping parts are sandblasted, surface burrs and oil stains can be effectively removed. It can improve the surface cleanliness of aluminum stamping parts. By controlling the blasting material, different surfaces can be obtained and the roughness of the product can be increased. Product performance can be greatly improved. In the subsequent surface treatment process, the adhesion between the aluminum stamping parts and the coating can also be increased a lot, making the product more durable and beautiful.
3. Polishing treatment
The polished aluminum stamping parts can be close to the mirror effect, which greatly improves the grade and aesthetics of the product. However, due to the characteristics of aluminum products, aluminum stampings require relatively little polishing. If no other surface treatment is performed after polishing, the durability of the product will be affected. Moreover, after aluminum stamping parts are polished, it is difficult to maintain the mirror effect for a long time. Therefore, if a mirror effect is required, it is recommended to use stainless steel as the product material.
4. Wire drawing processing
There are many types of brushed aluminum stampings, the most common ones are straight drawing, chaotic drawing, spiral drawing and thread drawing. After the aluminum stamping parts are wire-drawn, clear and delicate marks can be seen on the surface, and the product gives people the visual experience of luminous silk patterns.
Aluminum stamping parts basically require surface treatment after processing, but which treatment method is chosen depends on the customer's specific requirements. In the absence of customer request, anodizing is usually the default.
Why choose Xinzhe for custom metal stamping parts?
Xinzhe is a professional metal stamping expert that you visit. Serving clients worldwide, we have been specializing in metal stamping for almost a decade. Our exceptionally talented mold technicians and design engineers are committed, professional, and have a strict work ethic.
What's the key to our accomplishments? One term sums up the response: quality assurance and specs. For us, each project is distinct. We are driven by your vision, and it is our duty to bring that vision to pass. We attempt to comprehend every aspect of your project in order to achieve this.
We put a lot of effort into realizing your vision once we have a grasp of it. Along the way, there are several checkpoints. This enables us to guarantee that the finished product fully satisfies your needs.
Our group currently focuses on providing custom metal stamping services in the following fields:
Stamping in stages for both small and big quantities
Secondary stamping in small batches
tapping within the mold
Taping for secondary or assembly
Machining and shaping
If you would like more information, don't hesitate to get in touch with us.